Overcoming 6 Challenges in Panel Building and Control Manufacturing
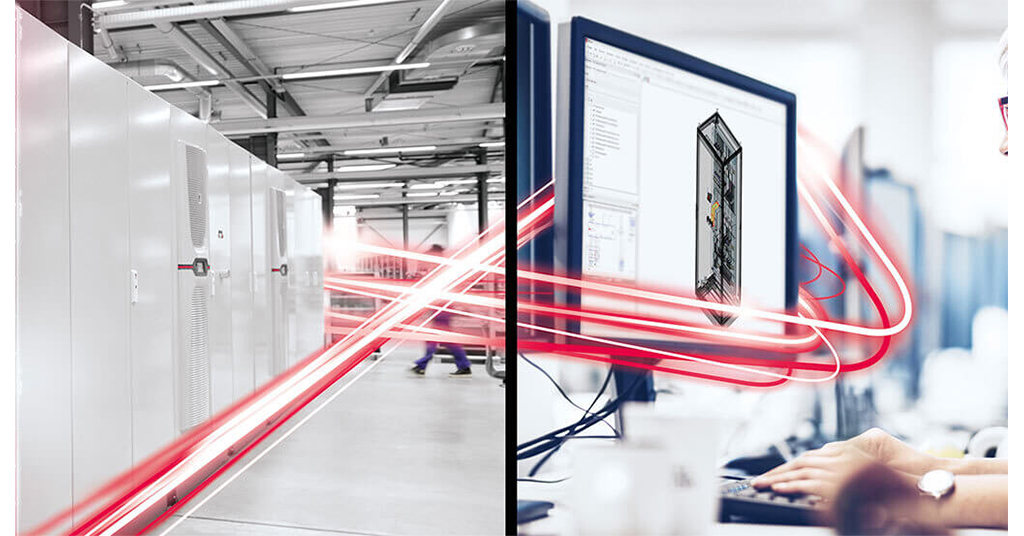
March 27, 2023
By Rittal North America
Rittal’s take of 6 challenges facing the industries of today
The manufacturing challenges of today can be overwhelming – from supply chain disruptions to increased customer demand, meeting production needs continues to get harder. Luckily, there is a better way to simplify the process.
By combining value-enhancing process steps in engineering, design, work preparation, production, and maintenance, it is possible to create a solid foundation for efficiency improvements. It’s time to optimize your company’s performance to deliver the most value for the least cost and enhance your competitive advantage.
Whether you’re looking to lower costs, take on more complex projects, shorten lead times, or work with limited resources you’re likely confronted by seemingly unsurpassable roadblocks. In this blog, we will explore solutions to overcome six common challenges that panel builders and control manufacturers experience by leveraging Industry 4.0 and IIoT technologies.
Rework or defects caused by human errors
Let’s face it, human error is inevitable. We’ve all been there – working too quickly and you miss a step, or something isn’t perfectly aligned. At face value it doesn’t seem like a big deal until you realize that all of the materials need to be scrapped. Now you’re at square one or more accurately, you’re already behind. That mistake has cost potentially thousands of dollars in resources. Not just the cost of the materials, but also the labor costs – how much time was invested that is now gone? How will those costs affect the next project in the line and each subsequent project?
Every error, defect, or rework has these costs associated with it. So, you must ask yourself, how much can you afford to throw away, how much can you afford to be behind? Most importantly, how does this one small mistake affect long-term profitability? Each of these instances will compile on top of each other, further increasing total costs, reducing profitability, lengthening timelines, and risking your competitive advantage.
To help eliminate human error from the production mix, automating processes is key. Having repeatable, accurate processes will streamline the workflow. Continuing to improve operations will help to ensure the longevity of your business while meeting the increasing customer demands.
Rittal Automation Systems utilizes technologies to optimize and automate your enclosure modification process. For example, hole drilling, thread-tapping, and cut-outs can be performed on state-of-the-art milling terminals, such as the Perforex, that can increase efficiency up to 85% compared to manual enclosure modification.
Lack of skilled labor
The U.S. has an aging workforce and expert technicians are retiring leaving a gap in skilled labor. Knowledge transfer – the sharing of institutional knowledge and best practices is challenging when there is high turnover or not enough incoming talent. It can take up to a year to train someone new on systems, procedures, techniques, etc. So how do you overcome this challenge when time is of the essence?
Automation can help support these transitions by storing needed data in an easy to access place, having systems that can provide step-by-step instructions, and even replace manual labor, and reduce human error found in manual tasks.
The Eplan suite of solutions enables users to input data at the beginning stage and all details will flow throughout the process from engineering to supply and manufacturing to operations. Eplan software integrates seamlessly into the Rittal Automation Systems machines making it easy to automate processes throughout panel building – drilling, tapping, and cutouts and streamlining the wiring process.
Costly delays in the production sequence
Redlining can be a manual and time-consuming process. You’ve spent weeks perfecting the wiring layout inside an enclosure making sure there is a path connecting each control and component, you send the design over for installation and it doesn’t work – a connector is aligned wrong, there was a change to the design layout, or something else that contradicts your hard work.
Now, it’s sent back to you for revisions. How far behind schedule does this put you, the team, the end customer? What if there was a better way to visualize the final outcome – see your design in 3D and know that there are no collisions throughout the design? You’re not dreaming, this can be a reality with EPLAN Pro Panel.
The electrical design for control enclosures, switchgear, and power distribution systems for energy distribution is available in 3D. The most diverse engineering tasks can thus be handled in just one software application – from electrical circuit drawing creation, via 3D planning of the mounting layout, through to virtual routing of the wiring connections. This technology helps to eliminate the guesswork and streamline the production sequence – all changes made in one part of the sequence will be implemented downstream.
Material waste and increased inventory
Since manual work is not as accurate as a machine completing tasks, technicians that are manually cutting wires tend to cut more than what is needed and / or make mistakes in the cut length. This causes an increased order of expensive wires and throwing out the wire scrap. This abundance of unusable wire can result in up to 20% waste! Do you frequently walk by that box of wasted wires and wonder how you can reduce it?
Transitioning to semi-automated and fully automated solutions throughout wiring processes can significantly reduce waste while making panel wiring more efficient including wire cutting, stripping, crimping, and more. Upgrading to automation will help to achieve the repeatability and reliability needed to produce wires at the desired length – reducing waste. Semi-automated cutting machines are easy to program and interface with Eplan software solutions.
Wire with diameters up to 10 mm 2 can be cut to length easily. Semi-automated stripping machines can strip wires with adjustable pull-off lengths from 3-20 mm and up to 6 mm2 diameters. Semi-automated crimping machines produce wire end ferrules with diameters up to 2.5 mm2 that can be quickly insulated and crimped. The fully automated Wire Terminal WT C enables wires to be processed from bulk with individual wire printing and then ready for assembly. The WT C offers flexible configuration, quick change system for wires, process reliability, three wire output methods, and a digitally supported process. Additionally, the WT C is adaptable and offers an expandable modular system structure to meet future requirements.
EPLAN Smart Wiring provides step-by-step instructions for easy implementation without schematics. It is your virtual assistant for manual wiring in enclosure manufacturing. From the connection point to the exact routing path, the software provides the wiring technician with all the necessary information in digital form – even in 3D when needed. You can determine whether the displayed installation connections are to be wired individually or in a fixed sequence and you can record the wiring using the traffic light principle.
All electrical schematics are available when needed and you can pass on any irregularities directly to the design department via e-mail. Providing project data on a central server makes it possible to produce many identical enclosures in parallel or to work together with several wiring technicians.
Looking beyond the wiring costs, it’s time to assess the enclosures on hand. How many times have new cutouts been needed on just the enclosure door, but the entire enclosure needs to be replaced? That’s a waste of material. What if you could just replace the panel? How much time would that save you and the end user while significantly reducing your overhead costs? Standardizing with freestanding enclosures that are bayable to support virtually any configuration will help you build solutions that meet the customer’s needs while reducing material waste and keeping the footprint to a minimum. Additionally, if the control configuration changes or a panel is damaged, you can easily replace the panel – leaving the original enclosure in place.
Now that’s a smart solution to reduce waste and save you and the end-user time and money! Further streamline processes with EPLAN Pro Panel which allows engineers to save data early in the preplanning / design process making it easy to reference all details and easily generate data sheets or specifications for materials procurement or access the data for use in downstream planning phases.
Mitigate injuries from manual work
Manual work can lead to injury especially when working with oversized and / or heavy items. You’ve heard the phrase “Work Smarter, Not Harder”, well it’s time to start adopting that approach. Finding ways to make lifting heavy items and working in tight tedious areas easier will promote a healthy work environment that reduces the risk of injury. Utilizing tools and equipment that help promote an ergonomic environment for technicians can help reduce stress on their bodies – leading to fewer injuries and enhancing the production process with less downtime.
Carrying heavy enclosures across the plant floor is dangerous – you risk injury to technicians and to the equipment. However, if you utilize the Smart Lifter, you can easily transport populated and bayed enclosures up to 3968 lbs. in weight and 15.75 ft. in length throughout the facility. The torque driven height adjuster can lift to a height of 9 in., allowing operators to fit the cable base / plinth and lower the enclosure onto pallets. The torque handle enables the entire system to be gently lowered into place and helps to protect employees from incorrect operation. With the Smart Lifter, enclosures can be easily moved more safely and with fewer technicians needed.
For flexible, efficient wire assembly and wiring work in the workshop, the wiring workstation is the ideal interface between the fully automated production of wires with the Rittal Wire Terminal and cutting / stripping wires by hand. The Wire Station WS 540 is an ergonomic process optimizer for use with all wiring-related activities. Customize the Wire Station with accessories including: wire storage, wire routing, equipment carrier for semi-automatic machines, socket strip, working lamp, mini-PC holder, monitor holder, tool and cup holder, wastepaper basket as well as magazine support for further processing of pre-assembled wires from the Wire Terminal.
Rising pressure to complete projects faster
Whether it’s concerns around stable supply chains, labor shortages, or customer demand, manufacturers will once again be tasked with discovering new methods of maintaining manufacturing cycles with an eye toward unlocking increased efficiency and reducing operational costs. Automation is key to these successes. For example, a wire terminal can help automate the manual wire creation process by completing several steps with one machine. It can produce different wires with cross-sections from 0.5mm2 to 6mm2 and print in different colors without retooling, cut to length, strip and crimp – without employee intervention, completing the process up to 8X faster!
Not only is the pressure on to complete projects faster, but there is growing demand for precision and repeatability throughout processes. Designed to provide end-to-end visibility and transparency from panel engineering to the production process, the synchronization of each individual step in the design and engineering process along with detailed reporting, real-time updates, and data / schematic storage and sharing helps automation architects overcome some of the more common stumbling blocks in the industrial manufacturing landscape; EPLAN eManage is your cloud-based foundation for active collaboration across projects and locations.
Quickly and securely share data with co-workers, partners, suppliers and clients. The solution allows you to easily upload projects from the EPLAN Platform or an internet browser into the EPLAN Cloud enabling quick response, detailed schematics, and repeatable processes – all information can be implemented again and again simultaneously across systems.
Using standardized enclosures will further help in completing projects quickly and accurately. TS 8 enclosures are modular – this allows you the flexibility to build a system by joining together enclosures of various widths instead of using a large welded unibody enclosure. The modularity of the TS 8 also allows for the easy expansion of the enclosure system simply by adding additional enclosures. Another benefit is that modularity allows you to modify or change individual components such as doors, sidewalls, roofs, or rear walls instead of replacing the entire unibody enclosure.
The TS 8 enclosure mounting panels, doors, and outer skins are interchangeable, if they are the same dimension – meaning you do not need to worry about which panel goes to which enclosure. Just install and go! You can create the cutouts on all enclosure panels and assemble them as needed. This means less space being taken up on the floor, less time spent matching panels to enclosures and the process can be repeated time and time again – even if a new door is needed in the future, it can be easily swapped out.
Bonus: Increase business with limited resources
Automate and industrialize panel building and control manufacturing with expert knowledge and combined solutions from Rittal and Eplan. The combined expertise allows you to establish solid foundations for automation solutions to streamline your enclosure engineering, sourcing, manufacturing, and operations.
Rittal and EPLAN help today’s manufacturers leverage powerful industrial automation equipment, software and tools to simplify the design and engineering process with powerful computer-aided engineering solutions that unify the control panel production sequence. With each phase of the panel design and production process clearly visible, manufacturers can create a connected value chain to react with more flexibility to shifts in production and scale their business.
A connected value chain helps machine builders, panel builders, and systems integrators spec the right solution for the right application with speed and accuracy into production processes for increased efficiency, speed to market, and growth.

https://blog.rittal.us/overcoming-6-challenges-in-panel-building-and-control-manufacturing