Panel Mounting Electromechanical Switches
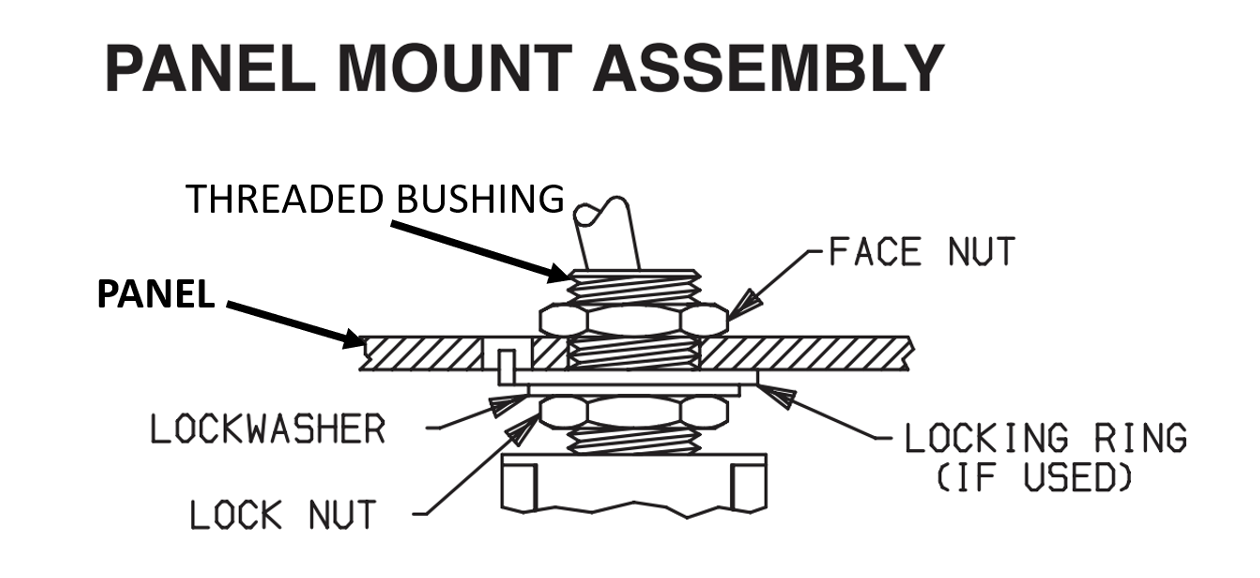
By Troy Dixon, Global Product Manager at Littelfuse
March 20, 2023
As technology and machinery evolve, the way we interface and interact with electronic equipment also advances. Many traditional human-machine interfaces (HMI) are updating to sophisticated touchscreen technologies. Even in a world where touchscreens are growing in popularity, they are not the right choice for every application. In industrial and construction settings, operators rarely see machines, instruments, or other pieces of equipment using touchscreens. This is because touchscreens are not suitable for applications and environments where operators wear protective gloves. This is where panel mounted electromechanical switches are used.
Market Overview
According to Global Market Insights, the electrical switch market size exceeded USD 13 billion in 2021, and is projected to expand at a CAGR of around 6% from 2022 to 2030. Technology advancements in automotive and off-highway vehicle applications, including autonomous driving and enhanced instrumentation & infotainment systems, are revolutionizing human machine interfaces (HMI). The proliferation of industry 4.0 and IIoT are increasing productivity and cost-efficiency, while making industrial applications safer for operators. Smart factories and robotics have changed the way switches are utilized, as well as the performance requirements of switch designs.
What kinds of switches can be panel mounted?
Many different switch types can be both PCB or panel mounted. Switches with higher electrical ratings are panel mounted because PC boards are not rated to handle high amp components. This typically includes, but is not limited to, toggle, rocker, push button, rotary, slide switches and switch locks.
Application Challenges
Switches are usually the first component to fail on an electrically controlled machine. Most industrial applications still require switches that offer some level of ingress protection (IP) to prevent failure from exposure to liquids, dust, vibration, shock, and extreme temperatures. IP ratings consist of a two-digit code, with each digit representing the protection range. The higher the number, the greater the protection. The first digit represents protection against solids. The highest rating is 6 (IP6X) and offers a dust-tight sealing. The second number is protection against liquid ingress. The highest number is 9K (IPX9K) and offers protection from high-pressure and high-temperature water spray. Switches with a higher IP rating offers higher reliability and longer operating life.
Size restrictions is also nothing new for many emerging applications including Industry 4.0 and IIoT. The switch is dictated by the electrical rating. Higher amp switches require a larger physical structure (internal and external) to handle the electrical load without failure. Switches designed for harsh environments also tend to have larger actuators to accommodate operators with gloves.
Tactile feedback through thick working gloves is also an important consideration. Positive detent in snap-action switches return distinct tactile feedback and make audible clicks when used on front panels, multi-function grips, and other switching units within the equipment. Some switches use two hall-effect devices for dual output within a single pushbutton or rocker switch housing where the output is linear in both directions. Other multiple-directional types come with one switch per direction for a single output or two switches for two-step actuation or redundancy. This type moves in four directions: up, down, left, or right.
Robust rocker switches often supply switching functions in off-highway vehicle dashboards and armrest controls because they typically survive more than one million cycles, yet are cost-effective. Such switches come with multiple actuators, different terminal styles, and mounting options to fit the application. Short-circuit protection (a ridge between the contacts prevents short circuits, even under tensile load of the connection cable) and integrated temperature compensation provide even further durability and reliability.
What kind of panel cutout is required?
The panel cutout is the mounting hole where the switch is attached to the panel. The type and size of the panel cutout is determined by the switch . For toggle, push button, rotary, and switch locks, the panel cutout is round. The diameter of the panel cutout needs to be large enough to accommodate the threaded bushing ‑ where the mounting hardware is attached. For rocker and slide switches, the panel cutout is rectangular. Round panel cutouts are most commonly drilled, while rectangular panel cutouts require a chassis or panel punch.
OEMs cut through the panel material and have an automatic centering design for accurate alignment. Regardless of the shape of the panel cutout, it is important to keep in mind the maximum panel thickness a chosen switch can handle. For round panel cutouts, the length of the threaded bushing needs to be taken into consideration. If the panel is too thick, manufacturers won’t be able to attach the mounting hardware.
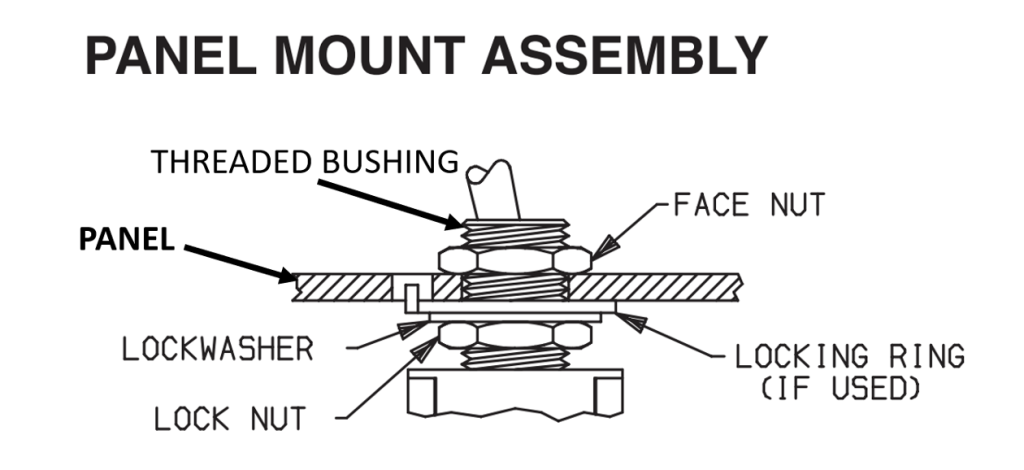
For rectangular panel cutouts the length and width as well as the panel thickness needs to be considered.
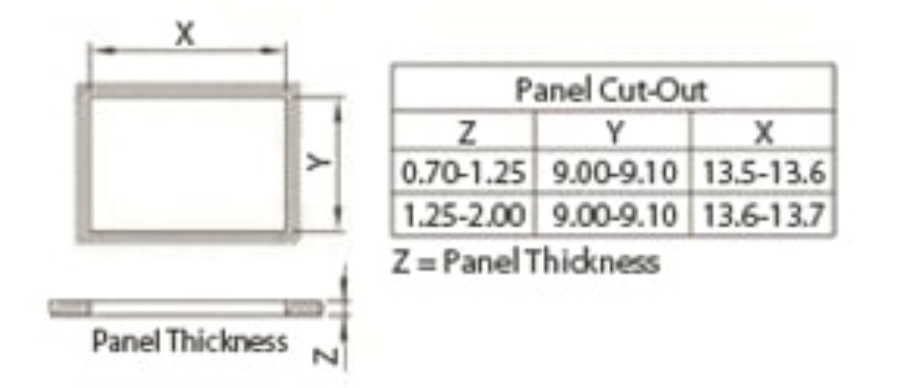
Snap in mount switches have a spring-loaded locking mechanism that opens as the switch is pushed through the panel cutout. If the panel is too thick, the spring-loaded locking mechanism will not be able to open and the switch will not be properly secured to the panel.
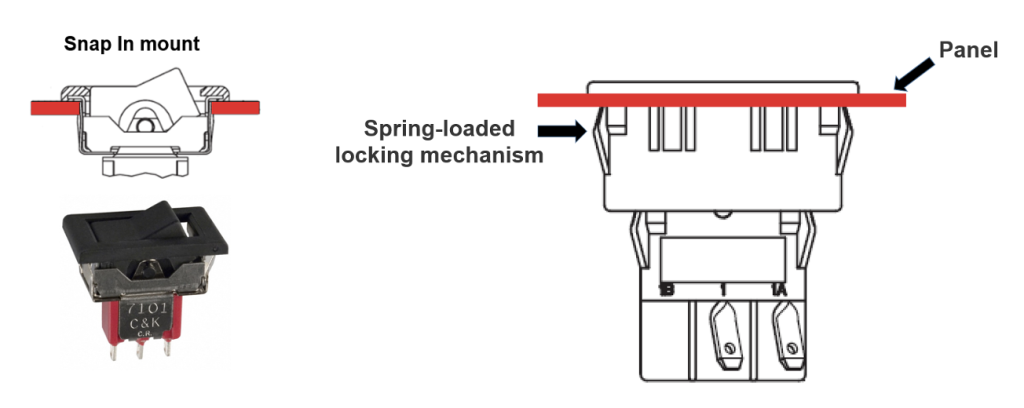
For sub panel mounted switches, additional holes are drilled on each side of the panel cutout. The switch is inserted from the bottom side of the panel and attached with mounting hardware.
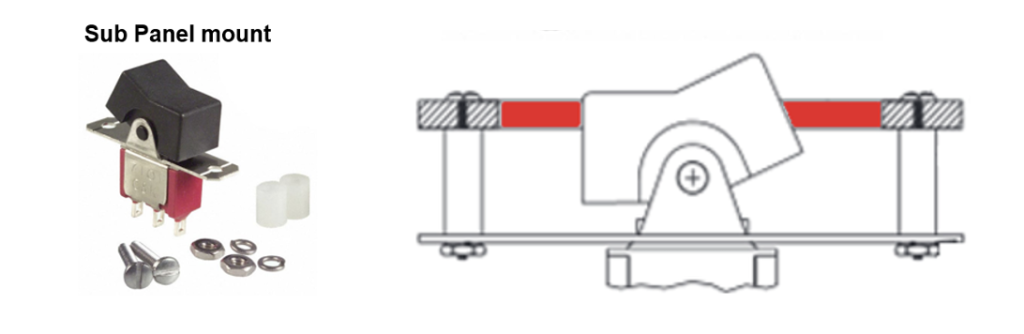
Wiring the switch in the panel
Panel mounted switches will have solder lug or quick connect terminals where the wires are attached to the switch. Solder lug terminals will have wires soldered to them.
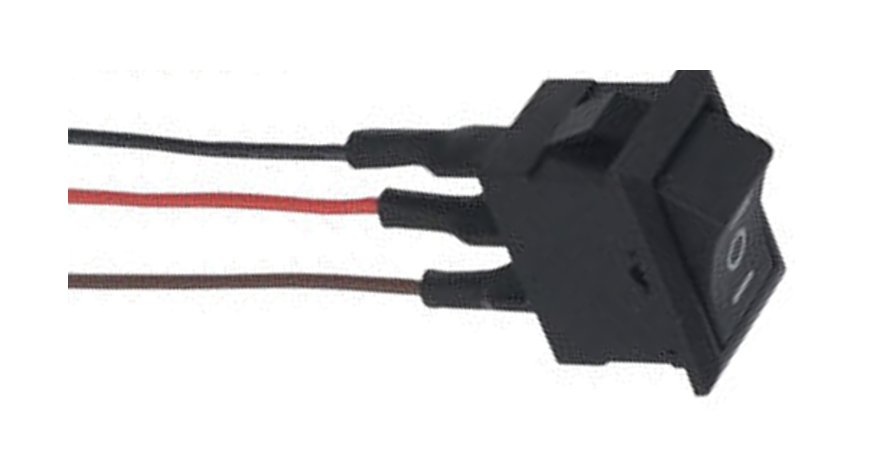
Quick connect terminals have connectors that crimp to the wires and slide onto the terminals.
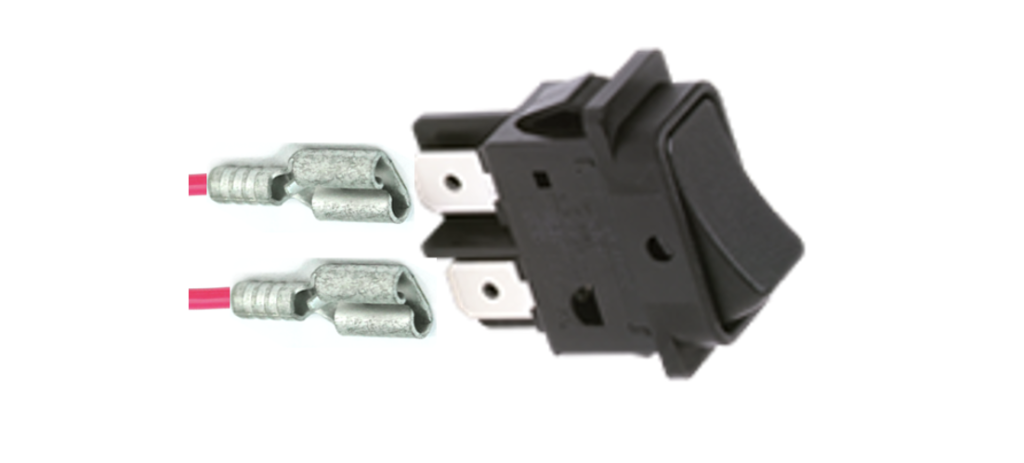
As mentioned previously, the physical switch size is often determined by the application’s required current rating. Low current (logic level) switching loads can be accomplished by physically smaller switches. However, an application switching a power supply using 3 A to 16 Amps will usually require a physically larger switch.
Low current (logic level) Toggle switch size vs. high amp Toggle switch size.
GT series, CONTACT RATING: 0.4 VA max. @ 20 V AC or DC max. (under 1 amp).
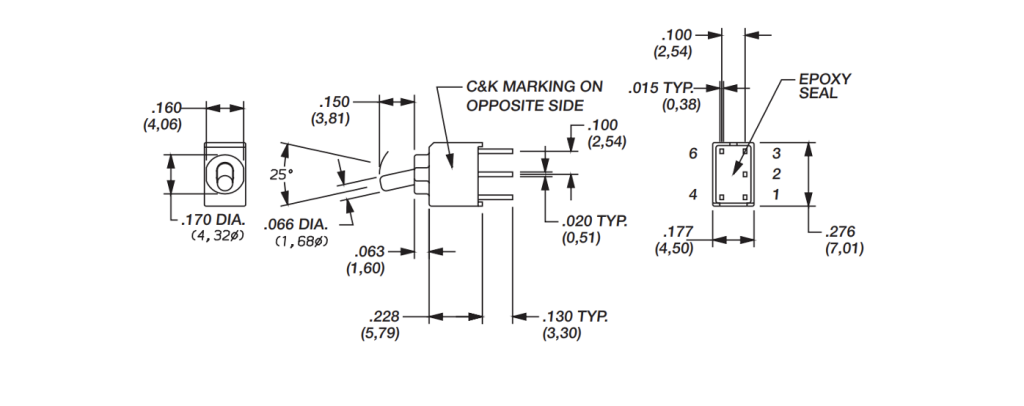
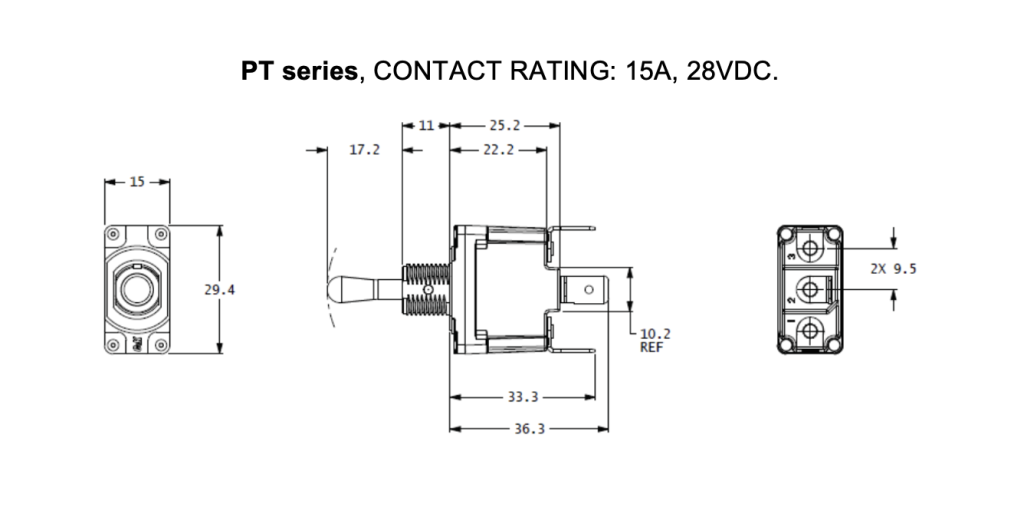
Conclusion
Original equipment manufacturers increasingly expect more than just standard panel mounted switches from electromechanical component manufacturers, they want customization options. Because switch manufacturers now deal with the entire module and dimensions are becoming more critical, they must work more closely with customers during initial design stages to satisfy all detailed requirements. By working closely with customers in all phases of the design process, switch manufacturers can identify materials that interface with the operator, and those in the actual contact mechanism can be re-evaluated and altered to conform to performance, reliability, lifespan, and robustness standards.