From Concept to Market: The First Ethernet-APL Field Switch for Process Automation
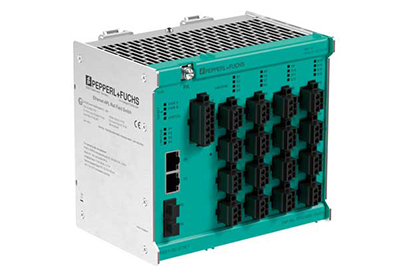
June 10, 2021
When it comes to Industry 4.0, the Industrial Internet of Things and digital transformation, the process industry —especially the field within the process plant—has been the blind spot of the industrial landscape. An innovative technology developed in cooperation with twelve companies and four standards organizations is finally putting an end to this: with the Ethernet Advanced Physical Layer, or Ethernet-APL for short, seamless, network-based communication from the field to the enterprise level is making its way into process automation. And with the Ethernet-APL field switch, Pepperl+Fuchs is now launching the first product worldwide that enables direct, fast, barrier-free access to and from the field instrumentation via Ethernet-APL.
For the first time, users in process plants are able to use well-known and field-proven Ethernet-based protocols such as PROFINET, EtherNet/IP or OPC UA beyond the control room in the entire plant. This opens up completely new applications for the process industry, such as those increasingly required in the context of Industry 4.0. But it also results in new automated processes for how users can work with instrumentation in the field of process plants in the future.
Simply Ethernet
The simplicity for which Ethernet is known as an established communication technology in our everyday lives is the focus in the development of Ethernet-APL: the Advanced Physical Layer makes standard Ethernet technologies available for the process industry and meets users’ expectations for simple, straightforward handling. Ethernet-APL is based on the robust and well-known two-wire cable and offers explosion protection with intrinsic safety as an integral part.
The existing cabling remains in place for re-use with Ethernet-APL based components, which considerably reduces the effort for modernizations or even for a complete migration from fieldbus to Ethernet. And this is where the Ethernet-APL field switch of the FieldConnex product family comes into play: in addition to Ethernet-APL, the field switch is the product that can optionally handle the Manchester Bus-powered Physical Layer (MBP) and can thus be configured quite flexibly to the installed base of PROFIBUS PA devices. It thus enables the concurrant operation of new APL and existing fieldbus field devices on a common infrastructure.
IIoT-enabled Applications and Even Higher Availability
Installation is quick and easy: the interface automatically detects and adapts to the communication physics of the connected device. It transmits power and data simultaneously on a two-wire cable into hazardous areas, in compliance with the requirements of the process industry. The Switch provides up to 24 ports for connection to APL-capable instruments or already installed field devices.
This gives the user access to multiple process values from a field device, such as volume, mass, temperature and density from a flow meter. Through a single infrastructure, the Ethernet-APL field switch makes all data from the diagnostics-enabled and highly configurable devices available to multiple applications simultaneously, enabling predictive maintenance of the device, plant and process. The Ethernet-APL rail field switch is mounted on the DIN rail in control cabinets or field distributors and can be installed in zone 2, the connections for field devices are intrinsically safe for zone 2.
The Right Switch for Every Plant Layout
This first Ethernet-APL rail field switch is perfectly suited for compact systems and indoor installations. In the future, the Ethernet-APL products will include a total of three different switches that support every type of topology. The Ethernet-APL field switch, which is powered by the APL trunk for outdoor installation up to Zone 1, is designed for system layouts with a larger footprint. The third variant, the Ethernet-APL power switch, is installed in the control cabinet. It supplies the APL main line with power.
Ethernet-APL Rail Field Switch – Highlights
Fastest and most efficient, barrier-free communication of large data volumes from the hazardous area to the cloud
- – Communication and power supply for Ethernet-APL instruments
- – Point-to-point connection to field devices via Ethernet-APL or PROFIBUS PA
- – Support of ring redundancy
- – Control cabinet installation in Zone 2 / Division 2
- – Intrinsic safety on the spurs: Ex ic IIC or Ex ia IIC
https://www.pepperl-fuchs.com/usa/en/44742.htm