Beckhoff: TwinCAT for the Process Industry
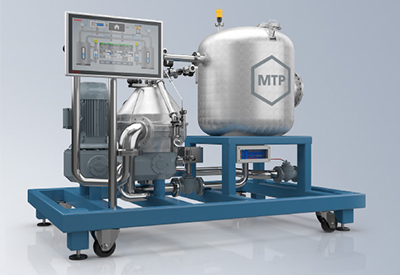
February 22, 2021
Module engineering with TwinCAT MTP
In TwinCAT, the MTP concept is built into the products TwinCAT MTP Runtime and TwinCAT MTP Engineering. TwinCAT Engineering provides project management capabilities, which incorporate TwinCAT MTP Engineering as a specific project type. This project type supports source code generation for PLC projects, which use TwinCAT MTP Runtime to create a standard-compliant interface in a process plant module.
Using the TwinCAT XCAD Interface option, code generation can be customized and the information made usable in other processing. Any changes made subsequently in the MTP project management system are incorporated through automatic project comparison.
The project can then be activated. The variables for the interfaces defined are provisioned to the POL automatically through TwinCAT OPC UA.
What is MTP?
Cyber-physical modularization makes it possible to build and adapt flexible process engineering plants with little effort. As a result, inflexible automation systems that have operated unchanged for many years are gradually becoming a thing of the past: Customization and flexibility are the way forward for the process industry.
An emerging challenge facing numerous sectors in the process industry, such as for example, pharmaceuticals, is the increasing fluctuation they are seeing across their markets. The pressure to achieve faster times-to-market is pushing them to accelerate development cycles. And, as product life cycles grow shorter, too, the ability to make customized products economically in smaller loT size is becoming essential.
One increasingly common approach is to build process manufacturing plants on a modular basis that gives them the flexibility to be reused. Here, a plant’s overall manufacturing process is segmented into sub-processes that are mapped to individual modules. To fully modularize the plant, a separate, decentralized controller is assigned to each module. The modules are then connected to a higher-level controller (a DCS, for example) that manages the overall manufacturing process. With this model, the focus of the development effort shifts from plant-centric to module-centric engineering – an approach that enables a plant to adapt flexibly and with little effort to changing requirements. New modules can be added to the plant, too, and existing modules reassigned or removed as necessary. Changes like these do not require plants to be completely re-programmed because most of the logic resides in the individual modules. The higher-level controller merely coordinates the modules and the services they provide, which is why it is described as the process orchestration layer (POL). In practice, this model is implemented to a vendor-neutral standard, the NAMUR Module Type Package (MTP), which defines how process modules must be described. An MTP, as defined in VDI/VDE/NAMUR 2658, contains all the information needed to integrate a particular process module into a modular process plant – incl. its functionality (in the form of services), communication specifications, and an HMI template. The interfaces defined in the MTP standard are designed to enable plug-and-produce operation, and so eliminate overhead when a processing plant is repurposed or reused. Thus, modules need only to be developed once, and can be incorporated into different plants, regardless of the controller vendor or POL.
Benefits of the MTP for the process industry
The MTP is a concept that can leverage optimization potential in process plants across the board, from planning to operation. This makes the MTP a crucial element in the development of future-proof automation systems.
Benefits of MTP
- – minimized plant engineering means faster time-to-market
- – short time-to-repair through unified module interfaces
- – module reusability enables custom production runs in small batches
- – numbering-up instead of complex scale-up procedures
- – HMI system with unified look and feel
Benefits of TwinCAT MTP
- – automatic code generation in compliance with VDI/VDE/ NAMUR 2658 standard
- – highly customizable for easy adaptation to existing processes
- – standard-compliant IEC 61131 function block library
- – simple MTP/P&ID import
- – seamless integration with TwinCAT Engineering
TwinCAT MTP highlights
- – integrated into engineering system
- – generates PLC template code in preparation of state programming
- – generates and exports MTP automatically
- – uses TwinCAT OPC UA on target system
- – can be combined with TwinCAT XCAD Interface