What You Need to Know About Lockout/Tagout Audits
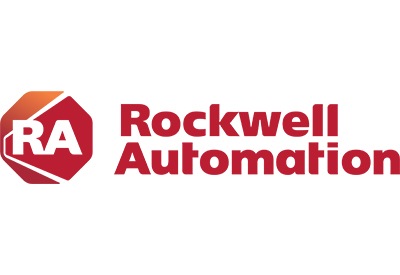
January 6, 2021
To maintain compliance with OSHA lockout/tagout standard 1910.147, it is required to perform annual inspections of both the procedures and employee competency in lockout/tagout practices. Annual audits are an important part of a lockout/tagout program because audits can reveal inconsistencies and problems.
When it comes to annual audits, there are three main steps to complete:
- – LOTO procedure audit
- – Authorized employee compliance review
- – Addressing any deficiencies in people, procedures, and processes
If you follow these three key components, your lockout/tagout program will stay up-to-date and compliant.
Review Your Lockout/Tagout Procedures Annually
The first step in an annual audit is to perform a review of all machine-specific lockout/tagout procedures. The purpose of the procedure audit is to identify any deviations or inadequacies in the current procedure. When you review a procedure, be sure to ask these three questions:
- – Is the procedure present and legible?
- – Are all energy sources accounted for in the procedure?
- – Does the procedure accurately represent the machinery?
First, verify that a procedure exists for the machine; make sure it is present and legible near the piece of equipment. If not, create or reprint the procedure.
Second, confirm that all energy sources are accounted for in the procedure and that no new energy sources have been added.
Finally, make sure that the procedure is still accurate, or has something changed since the last audit? Check the header information, and that the location of energy sources is still the same, or whether any energy sources have been removed. Has the equipment itself been relocated or removed?
Test Your Employees’ Competency by Watching Them Perform Lockout
The second component to a complete annual inspection is to review authorized employees. An authorized employee is a person who locks or tags out equipment to perform servicing or maintenance. Reviewing authorized employees performing maintenance will confirm that the employee knows how to follow a lockout/tagout procedure correctly and lock out a piece of equipment. The inspector who performs the review can be another authorized employee within your company, or a safety consultant from an outside company performing the audit.
The inspector should verify that the employee can follow the shutdown sequence of the equipment, place the locks and tags on energy isolation points, and follow the restore to service sequence. The inspector will also check that employees understand when to lock out equipment and how to handle special circumstances such as group lockout. Once the inspector is satisfied with the results of the employee review, this step is complete. You should complete this step for a reasonable sampling of authorized employees.
What if Deficiencies Are Found?
When performing the lockout/tagout procedure review, any inadequacies found in the procedure should be noted so that you can update the procedure accordingly. If a machine has been relocated but all energy sources are the same, the location of the unit must still be updated and the revised procedure must be printed off for use. Once updates are made to the procedures, the original procedures become obsolete, and any digital or hard copies must be replaced.
If new sources of energy are present or if existing sources are relocated, this needs to be updated as well. Even a new valve type or location of electrical disconnect should be noted. Finally, check for mistakes and typos, and anything that may affect the integrity of the procedure.
If deficiencies are found during an employee audit, retraining will be necessary. The retraining must be provided only to those employees who did not pass the employee audit and only needs to cover the sections they are deficient in. The retraining will re-establish the employee’s proficiency to use the lockout/tagout procedures. Be sure to make note of the retraining, as OSHA requires this to be recorded.
If most employees are found to lack the proper lockout/tagout knowledge, you need to undertake a more detailed investigation. The training module may need to be overhauled and all employees may need retraining. Enforcement of what is taught is critical for program success.
Audits Are a Key Step in Identifying Safety Risks in Your Facility
Lockout/tagout audits are pivotal to the success of the lockout program; without annual reviews, equipment modifications and employee deficiencies may never be caught. Spending time with employees and at the equipment can also be a great opportunity to identify other business needs and opportunities. Not only will completing the audits keep your company compliant with OSHA standards, it will also help protect the health and safety of all employees when they are performing lockouts.