Condition Monitoring Directly Integrated Into Control Technology
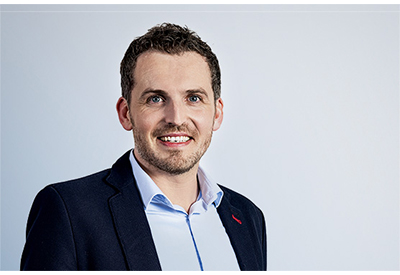
December 1, 2020
What characterizes ESR strain sensors?
Matthias Finke: The ESR series strain sensors are designed for permanent and temporary measurement of stress on practically all large structural components. What is referred to here specifically is their use in wind turbine rotors for supporting regulation of the individual blades. Other fields of use include load monitoring of cranes, material inspections and stress tests. The centerpiece of the sensor is an electro-optical position encoder, which has already proven its worth in many industries over decades. Particularly worthy of mention in this regard is the mechanical robustness coupled with a very high sensor resolution of 0.025 μm/m. In addition, an extremely broad measuring range of ±5,000 μm/m is offered as well as a maximum transmission rate of up to 30 kHz, which means that both static and highly dynamic applications can be supported. A highly integrated application-specific integrated circuit (ASIC) digitizes signals directly in the sensor, resulting in a low signal-to-noise ratio. The standardized EnDat 2.2 interface allows transmission of the incorporated electronic type plate and ensures comprehensive diagnostic capabilities. The ESR sensor series therefore represents the next evolutionary advance in digital strain measurement and the ideal basis for integrated condition monitoring.
What specific advantages are offered by the EnDat 2.2 Interface?
Matthias Finke: EnDat 2.2 allows a fully digital measurement chain to be realized from individual strain sensor through to the control and management levels. The interface is characterized especially by the following functions: Data can be transmitted at up to 30 kHz where needed at high frequency and in a highly deterministic manner as well as in real time over a cable length of up to 100 m. As a bidirectional interface, it allows data to be read from a sensor and also transmitted to the sensor. The interface is based on the established and robust RS485 physical layer, which means that sensitivity to external interference is low. The cyclical redundancy checking (CRC) ensures data is transmitted securely and any errors can be detected reliably.
How is the associated gateway structured?
Matthias Finke: Our understanding of a gateway is that the signals from multiple ESR strain sensors can be implemented on the fieldbus over the EnDat 2.2 interface. It is unimportant in this respect initially whether the relevant bus couplers and I/O terminals are mounted on DIN rail in an existing control cabinet (e.g. pitch system) or are implemented as a stand-alone solution in robust IP65 design for installation in the rotor blade root. The advantage of the gateway concept is that the system design is as simple, robust and cost-effective as possible. The EL5032 EnDat 2.2 interface from Beckhoff offers ideal support for this approach, since it is extremely compact in design and can connect to two strain sensors. The small footprint is especially beneficial with a system design involving multiple strain sensors. In addition, the EtherCAT I/O terminal fulfills our strict standards of quality and reliability just as with the EK9300 PROFINET-RT Bus Coupler.
What is your experience of bus couplers and the EnDat interface in practice?
Matthias Finke: Our experience with use in wind turbines has been extremely positive – worthy of particular mention in this respect is the installation location in the root area of rotor blades. System commissioning proved to be extremely easy, in terms of connecting both the ESR sensors and the PROFINET interface to the higher-level data recording system. This is especially true in relation to connection of strain sensors since no separate commissioning is needed on behalf of EnDat 2.2.
Which software functionalities are available for evaluating the ESR data?
Matthias Finke: We see ourselves as a sensor and system supplier in this field of use. We offer a scalable solution, which covers many individual applications from the ESR strain sensor to the EMS strain measurement system. Where ESR is used exclusively, full access is provided to the measured raw data of each individual sensor, while plausibility and monitoring functions as well as functions for calibration and calculating bending moment are available with EMS in addition to the hardware components for installation in the wind turbine. The C++ function library ESR eXtended is ideal for this scalable solution offering. We provide this library free of charge for TwinCAT 3 software. ESR eXtended is designed both to support system control in series use and for frequently changing measuring campaigns. Time synchronicity, signal reliability and system maintainability are determining factors for use in system control in relation to sensor signals and the information generated. ESR eXtended supports this with the following functions: full integration in PLC projects including all task classes, evaluation of sensor self-diagnosis, online plausibility checking of measured values and automatic importing of the sensor-integrated, digital type plate. Factors such as integration in measuring projects, reproducibility and straightforward documentation are especially important for use in measuring campaigns. The task class-integrated querying of measured values, including synchronous time stamp, also helps here.
Which TwinCAT features are especially beneficial for you?
Matthias Finke: We relied fully on TwinCAT 3 as the development environment for creating ESR eXtended. A particularly positive aspect here is that with TwinCAT 3, our function library has been provided with a digital signature, which guarantees the user a high degree of quality and traceability. Another practical benefit is integration in the widely used Visual Studio® tool, which simplifies familiarization. TwinCAT support for C++ likewise simplified the implementation of our function library.
Which advantages does Beckhoff PC-based control technology offer in General?
Matthias Finke: The openness of PC-based control is paramount here. For example, this means that it is possible to access the hardware even without the TwinCAT development environment, thus making it easier to change basic settings or access diagnostic functions. Furthermore, optimum support is provided for creating graphical visualizations, since familiar development tools can be used here. From the perspective of a wind turbine manufacturer, PC-based control allows direct integration of condition monitoring in the system control. This is necessary since processor-intensive algorithms are frequently used for structure monitoring. Comprehensive monitoring can therefore be established, which allows the entire drive train to be monitored from generator to rotor – in parallel with system control and using the same hardware.
What is your experience so far with specific customer projects?
Matthias Finke: As regards the fieldbus gateway, a number of measuring campaigns have already been carried out with the ESR strain sensor and the EL5032 EnDat 2.2 interface. Our experience and that of our customers has been positive, especially with respect to the fast integration and commissioning. An experienced TwinCAT 3 user can start a measuring project after just five minutes, in which all information concerning measured values, diagnostics and documentation has been recorded and processed digitally.
https://www.beckhoffautomation.com/english.asp?press/news5720.htm