How the Industrial Internet of Things Can Help Reduce Downtime
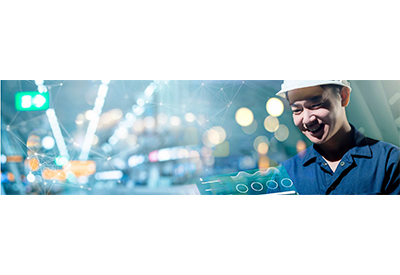
November 10, 2020
Unplanned downtime threatens productivity and profit across industrial and commercial sectors. In a recent survey of these customers, 20% rate reaching zero unplanned downtime as their top priority, and 70% consider it a “very high priority.”
Often, downtime comes as a surprise because facility operators lack visibility into their operations. Hardware failures and malfunctions account for 45% of downtime incidents – but 71% of field service decision makers aren’t fully aware of their assets’ maintenance schedule.
Mike Williams, Senior Product Manager at Hubbell® Wiring Device-Kellems, compares a traditional plant to a car without a tire pressure monitoring system. Drivers get little to no warning before a tire goes flat. “You weren’t aware there was an issue until you were on the side of the road jacking up your car,” he says.
In modern cars, tire pressure dropping by just one or two PSI will trigger a warning on the dashboard, so drivers know to schedule maintenance before they are left stranded.
Today’s industrial facilities are risking more serious consequences than a flat tire.
On average, a single industrial downtime incident costs $17,000. According to the International Society of Automation, facilities lose 5-20% of their productivity due to downtime. Customers who build airplanes and run large data centers stand to lose millions of dollars for each hour of downtime.
Preventing issues before they occur can lead to significant savings. But to predict problems, plant operators need actionable data about the equipment across their facility.
By connecting the plant floor through the Industrial Internet of Things (IIoT), they can remotely collect and analyze information about processes in real time and track trends.
Hubbell’s inSIGHT Data Monitoring System Creates a Smarter Plant Floor
Hubbell is the first electrical device manufacturer on the market to embed technology directly into their devices that can share critical information on key performance indicators – including currents, voltage and internal device temperature.
Electricity is a fundamental component of most industrial and commercial processes. Integrating intelligence at this level can provide valuable information across a broad range of applications.
“The failure modes and the pain points that everyone experiences are pretty consistent [across markets], and there’s a number of them we can address,” says Williams.
Whether they are manufacturing medicine or running a data center, customers want to maximize their uptime and efficiency.
Hubbell’s inSIGHT™ Data Monitoring system provides a flexible, scalable solution to gather and make sense of key metrics across a facility. It is compatible with any application powered by an electrical device, and inSIGHT devices are built and wired the same way as their non-smart counterparts. To add monitoring capability, electricians simply unwire a connection and rewire it with the corresponding inSIGHT device.
Customers don’t need to perform any complicated configuration; as soon as the device powers on, it can start sending data. Information is transmitted over a wireless mesh network, and signals can travel up to 30 meters between devices. A single gateway – which acts as the centralized hub of the system – can accept signals from up to 150 devices. Customers can view a range of real-time and historical data about their facility remotely through a dashboard.
Better Data Leads to Better Decisions
Armed with data, facility managers can become proactive instead of reactive. Just like a driver who gets an alert when their car’s tire pressure drops, they can schedule preventative maintenance and reduce costly and time-consuming unplanned downtime.
In addition to electrical data, the system can monitor environmental variables like temperature and relative humidity, and alert customers if they cross thresholds of normal operation. This capability is especially important for customers who depend on refrigeration. Williams worked with a restaurant owner who kept $10,000 of perishable food at a time in a cooler that regularly broke down. Another customer, a pharmaceutical manufacturer, typically inventories $2 million of raw materials in a refrigerated room. These customers can set up the inSIGHT system to send a push notification to their cell phone as soon as the temperature in their cold storage starts to rise.
Tracking data over time can also reveal slower-growing issues. As an HVAC system ages, for example, it typically requires more power to maintain a particular temperature and humidity level. However, its efficiency declines over months or years, making it difficult to pin down as the culprit when utility bills rise. By connecting their HVAC system and tracking its performance over time, operators can plan maintenance and upgrades in a cost-effective way.
The system’s reporting is over 99% accurate, which also allows for utility-grade billing in commercial applications. A typical colocation data center, for instance, bills customers for their energy usage by dividing the total utility bill by the number of renters sharing the space. Customers who use less power don’t benefit directly from the savings. By installing monitoring at the main power source, a facility manager can trace usage and bill customers individually.
For any facility operator, knowledge is power. IIoT solutions like Hubbell’s inSIGHT system provide visibility into equipment in real time and throughout its life cycle, helping to prevent costly surprises.
https://www.graybar.com/how-the-industrial-internet-of-things-can-help-reduce-downtime