How to Create Lockout Target Procedures
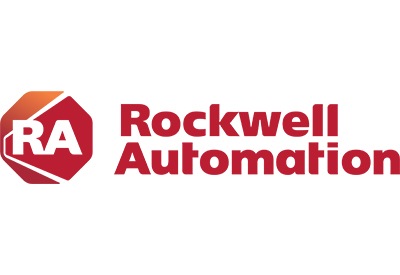
November 2, 2020
Lockout/tagout procedures, also known as energy control procedures, are used to establish a zero-energy state for safe servicing of equipment and machines. When considering lockout/tagout procedures, the first step is to understand what needs to be included in the procedure to achieve compliance and more importantly, to keep employees safe.
The control of hazardous energy regulation
The United States Occupational Safety and Health Administration (OHSA) established a set of guidelines that must be included within each lockout/tagout procedure. The list is as follows:
- – A statement of the intended use of each procedure
- – Procedural steps for shutdown and isolation of the hazardous energy
- – Steps for the placement, transfer, and removal of lockout devices, and the responsibility for them
- – Requirements for testing a machine to verify that the lockout has been completed properly
To satisfy the statement of intended use, it is best practice to specify who can use the procedure, when the procedure should be used, and the repercussions associated with failing to comply with lockout/tagout. When designing procedures for large quantities of equipment, this information is often built into a template used to make the procedures and is the same from one procedure to another.
In most cases, the procedural steps for shutdown within a lockout/tagout procedure include:
- – Notification to employees of the lockout
- – Normal shutdown
- – Isolation of energy and application of locks
- – Dissipation of residual energy
- – Proper verification of the zero-energy state
Also, there should be steps outlined within the procedure for proper restart of the equipment after the maintenance has been completed. OSHA specifications for removing the lockout include:
- – The machine and area should be checked to confirm it is operationally intact
- – The area should be checked to ensure that employees are safely away from the machine
- – Removal of the locks and restoring of energy
- – Notification to employees that lockout has been removed
These basic steps should be followed on each procedure, and the procedure for each machine must specifically instruct on how to fully isolate that machine. This means that each procedure must contain information for what energy sources the machine has, where those energy sources are isolated, how the energy sources are isolated, and how to verify the isolation.
Clear, quick instructions are key to LOTO succes
The key to making the best lockout/tagout procedures is to be able to communicate machine-specific information clearly and quickly to the user. It has been found that creating lockout/tagout procedures with a picture-based graphical approach allows for a 40% decrease in the time it takes to perform a lockout successfully. However, if the facility decides on a text-based format, then it is essential that the instructions and locations of the machine’s energy disconnects are clearly accessible and labeled.
Once the procedures are created, they must be accessible to the authorized employees who will use them. We recommend posting the machine-specific procedures at the point of use for the employees. An employee will be more likely to use the lockout/tagout procedure if is hanging on the machine and not in a binder in an office.
The main goal of lockout/tagout procedures is to establish the zero-energy state to protect workers from injury due to uncontrolled energy. Additionally, employing lockout/tagout procedures will help prevent harm to equipment and harsh lockout/tagout related OSHA fines. When creating and establishing lockout/tagout procedures, it is essential to include all necessary information that OSHA requires. Not only will the company be compliant with OSHA, but more importantly it will help ensure the safety of employees during maintenance.
Creating machine-specific lockout/tagout procedures for all required equipment at a facility can be a significant undertaking. Many companies find they do not have the resources required to complete this task in-house, so they often turn to outside help. Rockwell Automation has lockout/tagout specialists who create efficient graphical procedures and have helped hundreds of companies reach compliance with their lockout/tagout programs.