How Omron Can Help Electronics Manufacturers Prepare for Future Events Similar to COVID-19
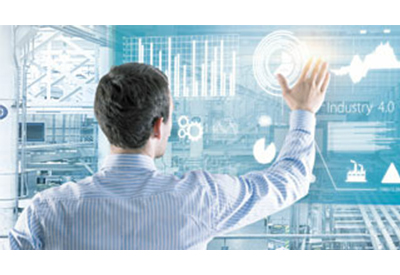
August 4, 2020
As the world reels from the immediate and secondary effects of the novel coronavirus pandemic, electronics manufacturers are struggling to enforce social distancing and protect their team members by finding ways to have fewer people in a working area at any given time.
One of Omron’s biggest goals as an automation supplier is to help companies allocate manual labor in the most efficient way while minimizing their team’s exposure to any hazards, including infectious disease. By strategically introducing automation, manufacturers can keep their employees safe and let them focus on less-repetitive tasks while improving productivity.
Here are a few automation technologies that can help ease the stress caused by COVID-19:
1. Remote management technologies
With advanced technologies that let you manage your operations remotely, there’s no need to be present on the factory floor to gather data from sensors and other components or program your PLCs. These things can be done from anywhere in the world, making social distancing concerns irrelevant.
Omron’s powerful Sysmac Studio allows you to remotely configure complete automation systems with subcomponents, including PLCs, sensors, motion control, machine vision and safety. It’s easy to set up and read data via a number of industrial protocols like OPC UA, EtherNet/IP and EtherCAT.
2. Predictive maintenance solutions
Many electronics manufacturers rely on regularly scheduled inspections of critical equipment in order to determine maintenance needs. Unfortunately, this strategy can cause any issues that arise between inspection dates to go unnoticed and can lead to unnecessary downtime. Omron’s solution is to bring in technologies that can monitor equipment health on a 24/7 basis.
Omron offers artificial intelligence (AI) solutions for predictive maintenance as well as a variety of sensors and other means of around-the-clock monitoring. One option for continuous electrical panel observation is Omron’s K6PM thermal condition monitor, which reduces component failure-related downtime and makes equipment health visible remotely.
3. Robust traceability systems
To support social distancing during the COVID-19 era, it helps tremendously to have complete visibility into production processes and the location of all works-in-progress. For instance, it’s much more efficient to have an automated method for knowing whether certain PCBs have gone through the testing process than it is to have employees manually keep track.
Omron’s MicroHAWK barcode readers are the perfect tools for traceability with the user-friendly WebLink interface that lets you enter a reader’s IP address on any web-enabled host to start decoding right away. Reader controls can be adjusted remotely whenever you need to make changes to PCB composition, and you can monitor results in real-time.
4. Collaborative and mobile robots
To support social distancing, it’s a good idea to replace drawn-out and tedious tasks with robotics, as this also improves productivity. While it may be impractical to install large-scale industrial robots, collaborative robots like Omron’s TM Series (which can safely work alongside a human operator) can dramatically ease the burden of repetitive tasks.
An excellent example of a common industry task that can be improved by introducing collaborative robots is PCB in-circuit testing. When done manually, employees spend large amounts of time waiting for the test to complete before removing the board from the machine and loading the next one. Automation allows employees to cover more creative tasks.
In a similar vein, mobile robots like Omron’s LD Series can automate repetitive and cumbersome materials transport tasks like moving supplies from the warehouse to the manufacturing station. Mobile robots can also be the foundation for automated disinfecting systems, such as those that use UV light to sterilize the plant floor.
https://automation.omron.com/en/us/blog/automation-to-adapt-to-covid