Sensors and System Maintenance in the Fourth Industrial Revolution
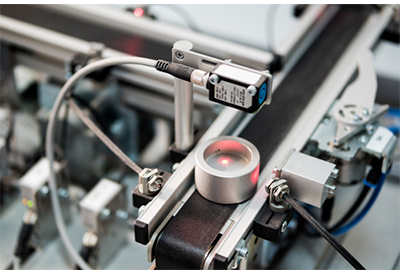
August 4, 2020
The fourth industrial revolution, or Industry 4.0, builds off the computerization and digitization of previous shifts and employs artificial intelligence, IoT, cloud computing and remote dashboards that measure and monitor parameters and minute data points related to industrial operations.
Industry 4.0 offers endless possibilities as more production lines are designed and configured with quality sensors. Those who utilize the right sensors, in the right place, for the right amount of time should experience improved system maintenance..
Such maintenance affords today’s production landscape and its many stakeholders improved maintenance possibilities. It comes about through predictive or scheduled maintenance, via an early warning for imminent, unplanned maintenance.
As more firms embrace Industry 4.0, compliance standards for networking connected devices will need to be implemented. IO-Link, for example, is an industrial communications networking standard (IEC 61131-9) commonly used to govern the connections of digital sensors, actuators and other devices with a digital platform to consummate industrial automation and enable scheduled maintenance.
Automation allows plant and equipment managers to better measure equipment and system wear, degradation and performance. With this information, managers gain visibility and control of an industrial environment, as well as improved maintenance.
Through information gathering and aggregation, voluminous operational performance data may be captured and analyzed via sophisticated business analytics. This allows for accurate predictions of when parts, machinery and other equipment may be due for service or replacement.
Scheduled Versus Unscheduled Maintenance
Scheduled maintenance on a part, equipment or system is proactive, but often static, and based on history and the manufacturer’s recommendation. The service may include assessments such as vibration monitoring, oil sampling and analysis or other action performed on the equipment or system. This may lead to a maintenance action or part replacement.
Unscheduled maintenance is obviously an unplanned activity and can be troublesome from both a timing and cost perspective. With Industry 4.0, better dashboards, virtual monitoring and digital twins (a virtual replication of a system, machine or other physical entity) aggregate more data, in real time, with good sensing. These tools help users avoid unscheduled maintenance.
A maintenance schedule, when accurately created, leads to a better use of automation, sensors and network-connected devices.
Such maintenance may include programs like vibration monitoring, fluid sampling, data gathering and analysis. Data logging is used to record parameters such as temperature, pressure, throughput and anything else that can be physically measured. Applying algorithms and machine learning to such data can help detect degradation or early signs of failure. Information retrieved via sensors and connected devices feeds into programs that work in tandem with maintenance schedules and predetermined maintenance requirements – usually through cloud-based software integrated with a remote user-friendly platform.
Today, there are countless sensors able to detect almost anything – motion, light, temperature, current, proximity, position, ultrasonic vibration and much more. They are part of the newfound industrial landscape where input and output become the basis of monitoring and measurement. Maintenance is now more predictive and scheduled than ever before.
When sensors, IoT and remote platforms converge, they help industrial operations stay ahead of operational trouble and material failure. Manufacturers avoid unplanned maintenance, failures and lost productivity. Accurate monitoring and greater efficiency are achieved through fewer operational interruptions.
Automation for Quality and Efficiency
As more companies embrace Industry 4.0 and automate the production floor with high-quality sensors, actuators and other connected devices like wireless piezo sensors that measure vibration levels and report those measurements back to the mainframe where the information can be acted upon, maintenance on the production floor will improve.
“Automation customers want to produce products at an increased rate, with higher quality, and be more efficient doing it,” says Russ Freeman, product portfolio manager with Allied Electronics & Automation in Fort Worth, Texas.
“No matter what control platform they choose to accomplish these goals, they are all dependent on repeatable, high-speed and accurate feedback from their sensors.”
Operational performance improves through better monitoring and accurate prediction of maintenance intervals. Time-to-failure becomes clearer. With good historical data acquired through quality sensors and connected devices, useful information becomes available to help drive better decisions on the production floor.
https://expert.alliedelec.com/expert-advice/sensors-and-system-maintenance/