GearSmart? Sales Reps Give Contractors an Edge in Power Distribution Projects
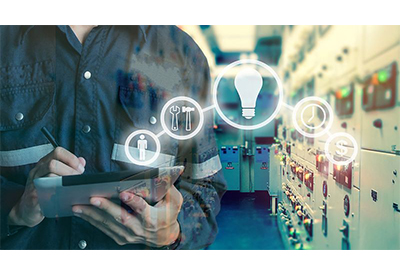
April 13, 2020
With electrical engineers in short supply as power distribution projects get more complex, Graybar trains GearSmart? sales reps to fill in the gaps.
When a major big-box retailer expanded to Nashville a couple years ago, the contractor in charge of the project quickly spotted a missing piece in the plans.
While the specifying engineer had started designing the power distribution system for the 1.5-million-square foot facility, they had left it for the contractor to complete.
“We were probably at a 30 percent design development package,” Jonathan Bartsch, a Business Development Manager at Graybar Nashville, remembers. “There were some pretty significant holes in there that we had to fill out.” Together, he and the contractor worked through the non-scheduled loads in the switchboards, and figured out how to feed new conveyers the end customer planned to install.
“Being involved on the early side, I could work through the best solution to reach what the end customer needed.”
In the past, electrical engineers were responsible for the technical work of designing a power distribution system. However, many general contractors and architects have trimmed engineering staff to reduce expenses, shifting the technical responsibility to contractors themselves.
Meanwhile, power distribution technology is getting more complex. Intelligent building applications, such as “smart” panel boards that automate lighting controls and track energy usage, require new skillsets from installers.
Faced with incomplete specs on complicated projects, contractors look to the manufacturers and distributors of switchgear for help.
Graybar saw the opportunity for sales reps to get involved beyond the bill of material. By providing advanced technical support earlier in the lifecycle of a power distribution project, they can help streamline the process and save contractors time and money.
Graybar recently teamed up with a leading manufacturer of power distribution equipment to provide select sales reps with specialized “GearSmart?” training. These sales reps are in a unique position to leverage strong relationships with both contractors and gear manufacturers. They provide support throughout the lifecycle of a project, ensuring it runs smoothly and turns a profit.
GearSmart? training unites in-depth product knowledge with Graybar’s logistics experience. These reps can work closely with a contractor’s estimating and project management teams, as well as the manufacturer’s field office, to secure the right material at a competitive price.
Jonathan Bartsch was one of the company’s first gear specialists. He joined Graybar in 2012, and has been in the industry for over two decades. He started working for a major gear manufacturer right out of college, making motor control centers in their South Carolina plant. Over the next 14 years, he moved from operations to marketing, where he priced gear being sold into the field, and then into sales.
“Things were a lot different back when I first got into the industry,” he says.
Today, the plans arriving on his desk are often incomplete or over-engineered.
“Incomplete or inconsistent drawings lead the person that’s doing the take-off to either do one of two things,” he says. “If they see that there’s a hole on the single line and they know something should be there, but they don’t know exactly what it is, they can either throw some money at it to cover it – or they can take the opposite approach, and they can basically exclude or clarify what the issue is.”
If a bill of material is missing important information, it can be underpriced. On the other hand, a “better safe than sorry” approach leads to an over-engineered BOM that adds unnecessary cost and complexity to a project.
“Engineers are short-staffed. They’re working faster to get things done,” he says. “In the absence of information they will choose the more costly option, because they know that they are quote unquote covered.”
Sometimes engineers will “gold-plate” plans by increasing the available fault currents, using special paint or calling for extra high efficiency transformers. Or, they might simply copy boilerplate specs from a previous job.
Having an extra set of expert eyes involved throughout the lifecycle of the project, from concept to plans to the quote, can save a contractor from unnecessary costs and headaches.
Sometimes, a sales rep can find significant savings by going back to the drawing board.
Last year, a water utility plant that has been in operation for over 60 years asked Jonathan for help replacing an aging motor control center (MCC) in their main electrical room.
Jonathan walked through the facility with the maintenance crew, and noticed that they had a full SCADA system and motor starters further into the system, closer to the motors themselves.
“Are you using any of the controls that are in the MCC that you want replaced?” he asked.
“Well, no,” they answered. “All we’re doing is using those as feeder units to the other starters that are inside the system.”
Jonathan realized that instead of installing a replacement MCC, all they really needed was a distribution panel board to feed the starters they already had.
On Jonathan’s recommendation, the facility decided to purchase two distribution online panel boards, at a quarter to a third of the cost of a new MCC.
“The value we provide … is to go back through and review those bills of material and make sure that you are getting what you want, what’s intended and what adds value to the project,” he says. “Our value to both you as the electrical contractors, and the industrial end customers, is to make sure that it goes as smoothly as possible on the contractor side, and that we can help you maximize your profit on the job.”